How Can Cold Spray Help Restore Damaged Aircraft Components?
It’s no surprise that aircraft endure extreme environmental conditions. Most aircraft materials and components wear over time. It’s almost inevitable that aircraft will require repair. It’s great to understand the types of corrosion wear and damage that your plane might face. When you need help preventing or repairing aircraft damage, Mid-America Aerotech’s Cold Spray process is an innovative and fast surface repair solution.
Corrosion Types Fall Into Two General Categories: Direct Chemical Attacks and Electrochemical Attacks
Electrochemical attacks are the most common form of corrosion and this type of electrochemical reaction is responsible for most forms of corrosion on aircraft structures and components.
An electrically conductive material, such as water, is required for an electrochemical attack to occur. When metal surfaces of your aircraft come into contact with a corrosive agent through a conductive path, corrosion begins.
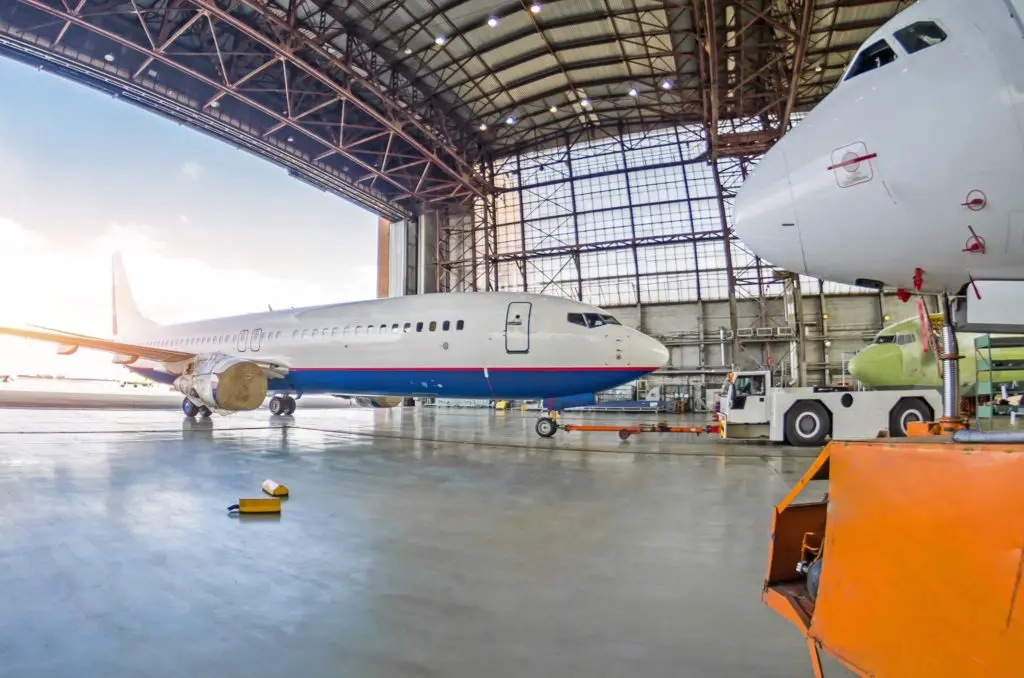
Cleaning your aircraft’s surfaces is the first step against fighting corrosion, and regular surface maintenance can keep your aircraft safe from an electrochemical attack. Removing conductive materials eliminates the possibility of an electrical current corroding the metal. Corrosion cannot occur unless a conductive material and a corrosive agent are present. By cleaning the surface regularly, you prevent this common type of corrosion.
A direct chemical attack is also known as pure chemical corrosion, and this chemical attack occurs when a bare surface is exposed to a caustic agent.
There are a few caustic agents that commonly cause corrosion of aircraft. Spilled battery acid, fumes from batteries, flux deposits from inadequate welding practices, and caustic cleaning solutions are just a few examples.
Taking a Proactive Approach Against Direct Chemical Attacks
With the introduction of closed unit batteries, leaked acid or fumes pose less of a problem for your aircraft.
Flux agents attract moisture and can cause severe pitting corrosion. If you are welding any components in your aircraft, be sure to remove all flux agents after the repair is made. Keeping surfaces free of thus debris is integral to corrosion prevention.
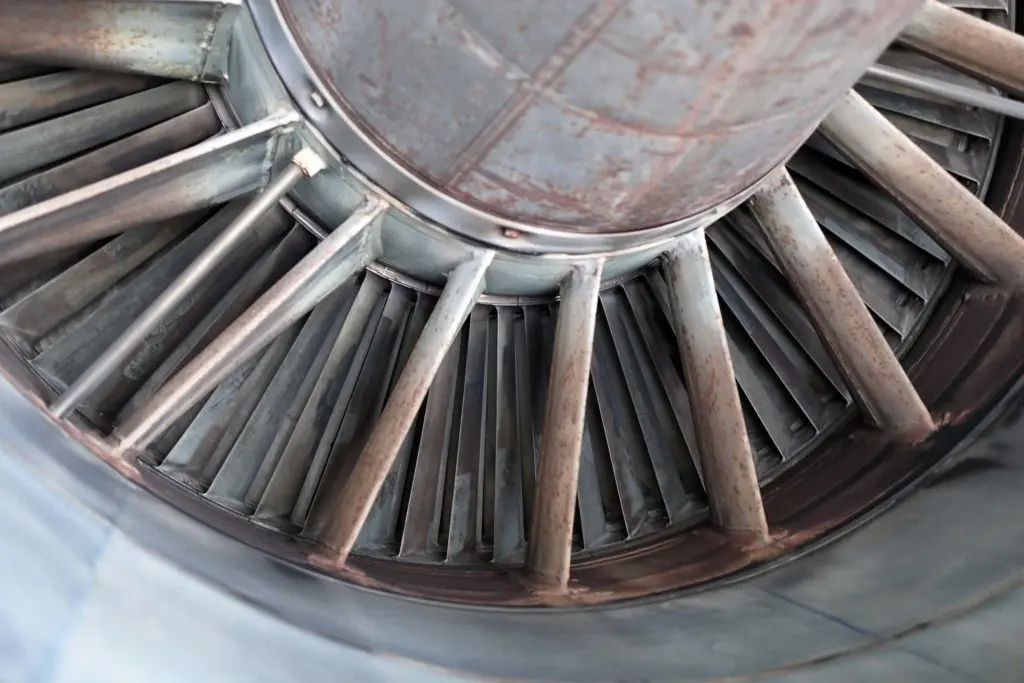
Use non-corrosive cleaning solutions during aircraft repair; although they may be less effective, using a gentler cleaning product on your aircraft will save you stress in the long run.
Aircraft Also Experience Structural Fatigue
After constant use and inevitable aging, metal in aircraft becomes weakened.
This weakening is called structural fatigue, and it will eventually require attention and possibly costly repair. If aircraft fatigue goes unaddressed, it puts the aircraft and passengers at extreme risk.
Structural fatigue first appears as tiny cracks in the metal’s surface and time further aggravates these microscopic cracks. As the aircraft is exposed to the flight environment, the cracks split wider. This destruction can lead to parts of the aircraft fracturing or splitting off during flight.
Where On An Aircraft Are Corrosion and Fatigue Likely to Occur?
Corrosion is likely to occur in areas exposed to the elements and corrosive materials.
The US Federal Aviation Administration outlines more than a few areas prone to corrosion on an aircraft. These components include the propeller surface, propeller hub, cylinder fins, areas around fuel tanks or bladders, control hinges, and the battery box. Surface seams and joined areas are also likely to harbor corrosive materials and begin to degrade.
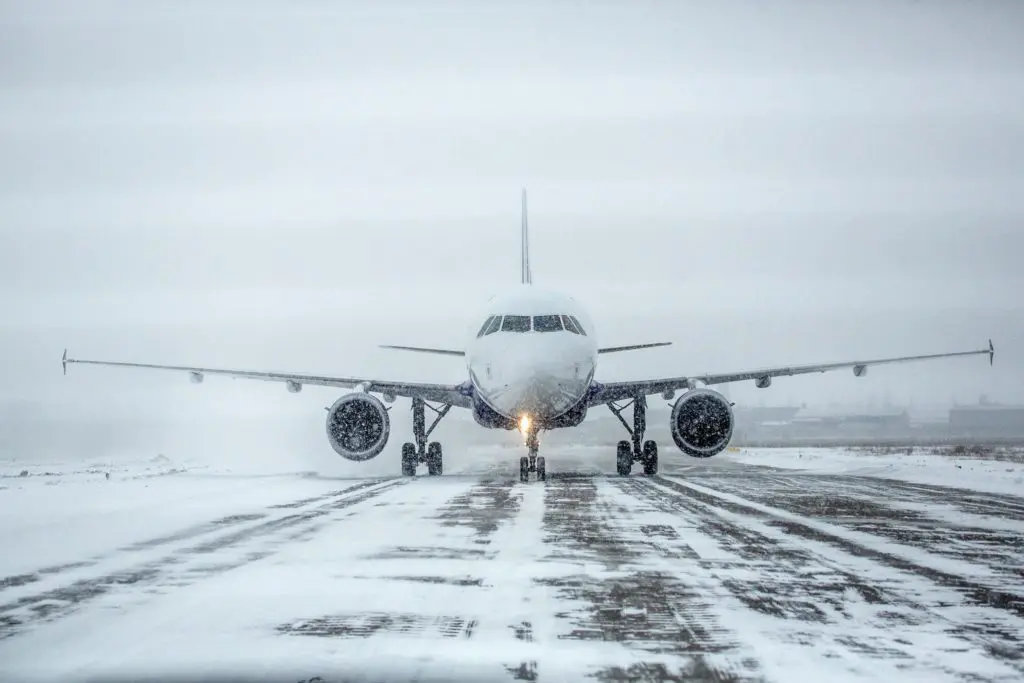
Metal fatigue can occur in almost every area of an aircraft.
Not unsurprisingly, fatigue can occur in an aircraft’s internal structure. These load-bearing elements have the potential to develop fatigue points under the stress of flight. This stress leads to necessary component repair or replacement to keep the aircraft in flying condition.
The external surface of an aircraft can also experience fatigue.
If structural movement or a heavy load stresses the skin of an airplane, the surface can begin to show signs of fatigue. These cracks can grow and lead to extremely dangerous conditions that require intervention and repair.
Metal fatigue can also occur in concentrated areas of stress. There is an area of concentrated stress around the edge of fastener holes. These spots endure high-pressure conditions while holding components together.
As time passes, the site of concentrated stress becomes fatigued, and tiny cracks begin to form.
How Can You Prevent Corrosion or Repair Damaged Components?
Abrasion can be used to remove light corrosion.
But, sanding away the lightweight surface corrosion is only the first step. You need to ensure that the corrosion won’t come back quickly.
Surface coatings will help prevent corrosion. You must apply a corrosion inhibitor such as paint, special emulsifying sprays, or a metal coating. An innovative coating solution is cold spray.
Cold Spray: Protection and Strength For Your Aircraft
Cold spray is an additive manufacturing process that creates a durable and protective coating on your metal surfaces. It is a wonderful solution for aircraft repair and structural component repair.
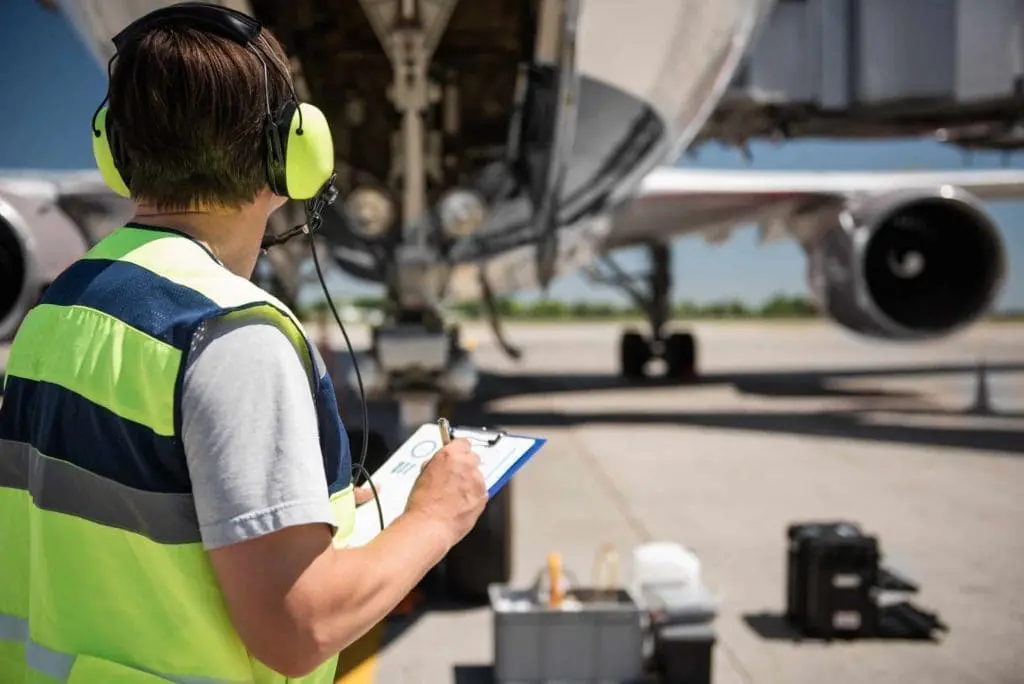
Applying cold spray is a fast approach for surface corrosion prevention.
Instead of replacing panels or undergoing other particle coating methods, you can use cold spray to repair damaged surfaces quickly. Cold spray can be applied in-situ and does not require extra curing times or part removal.
You can use cold spray for component repair to build up damaged parts.
Because it is an additive manufacturing process, you can apply cold spray in a concentrated area to rebuild heavily damaged parts and surfaces. Even large surface areas can be coating quickly with cold spray technology.
Surfaces coated with cold spray are tough and the particles from cold spray are deposited on your substrate at an extremely high velocity. This process creates a durable coating because each particle deforms to generate millions of tiny mechanical bonds.
No melting occurs during the cold spray coating process. The lower processing temperature of cold spray means that the structure of your aircraft components is not compromised during the repair. Cold spray coatings are made up of a variety of metallic and nonmetallic materials. It is technically a thermal coating process, but temperatures never rise high enough to melt the metal particles.
Cold Spray As A Highly Effective Solution For Corrosion Repair and Wear Prevention
If you work in the aerospace industry, you know that maintenance and repair are integral parts of the business. The skilled technicians Mid-America Aerotech are excited to show you how our Cold Spray technology can prevent corrosion and repair aircraft damage.