The Dangers of Intergranular Corrosion on Aircraft
Intergranular corrosion on aircraft is one of the primary reasons for catastrophic intergranular fracture. By preventing and treating aircraft corrosion, one can extend the life cycle of their metal components and keep your aircraft aloft.
After a thorough, certified inspection, take measures to repair intergranular corrosion by contacting Mid-America Aerotech for effective cold spray technology repairs.
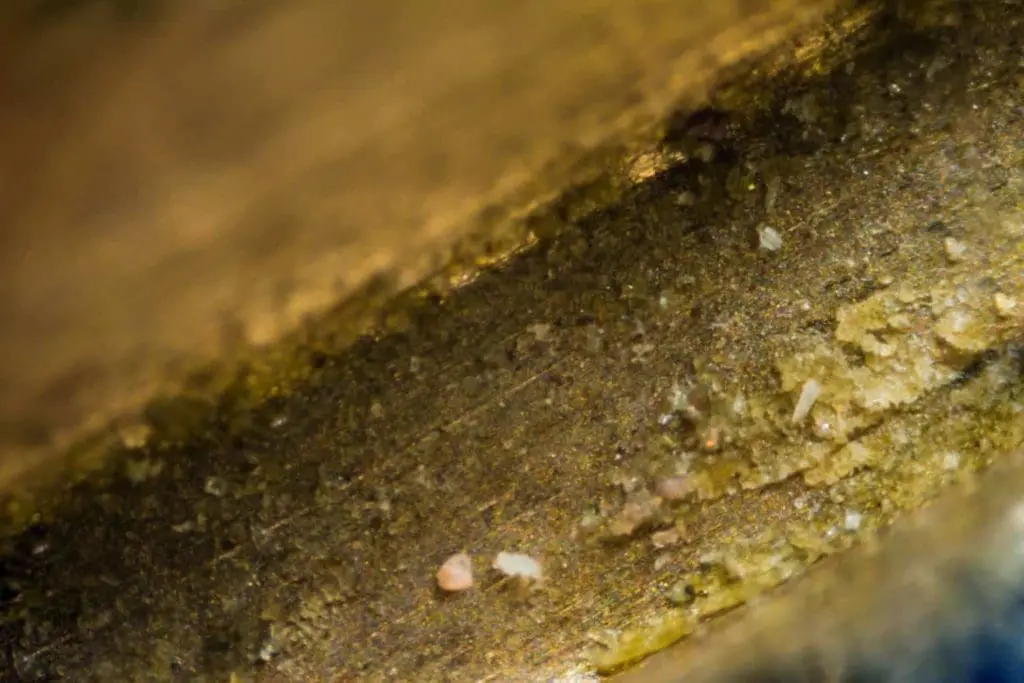
What Is Intergranular Corrosion?
Most metallic parts have grains (sometimes called crystallites) in their microstructures, the exception being monocrystalline parts, which are highly specialized and expensive components. They are mainly found as turbine blades. Grain sizes vary widely but are commonly much less than 1mm for aircraft structural materials. This means that any component contains a huge number of grains along with the boundaries between them. Intergranular corrosion occurs at this boundary or interface between two or more grains in a metal, leaving the internal portions of the grain unaffected. This localized attack can also happen next to grain boundaries.
Because intergranular corrosion happens at such small sizes, it is difficult to detect. It cannot be found by visual inspection, and destructive testing is not an option. Thus non-destructive testing is required to detect such corrosion before the component fails.
How Does Intergranular Corrosion Occur?
Intergranular corrosion occurs in several families of metal alloys. Some causes of it include:
- Porosity forming around the grain boundary
- Hydrogen embrittlement
- Impurities deposited at the grain boundary
- Corrosive environment
- Alloying elements diffusing to the grain boundary
- Grain boundary cavitation
- Precipitation of the second brittle phase at the grain boundary
In each instance, the grain boundary becomes the path of least resistance for cracks to propagate, similar to how cracks may propagate through the mortar in a masonry wall while leaving the bricks intact. When intergranular corrosion happens, grains may dislodge as the grain boundaries deteriorate.
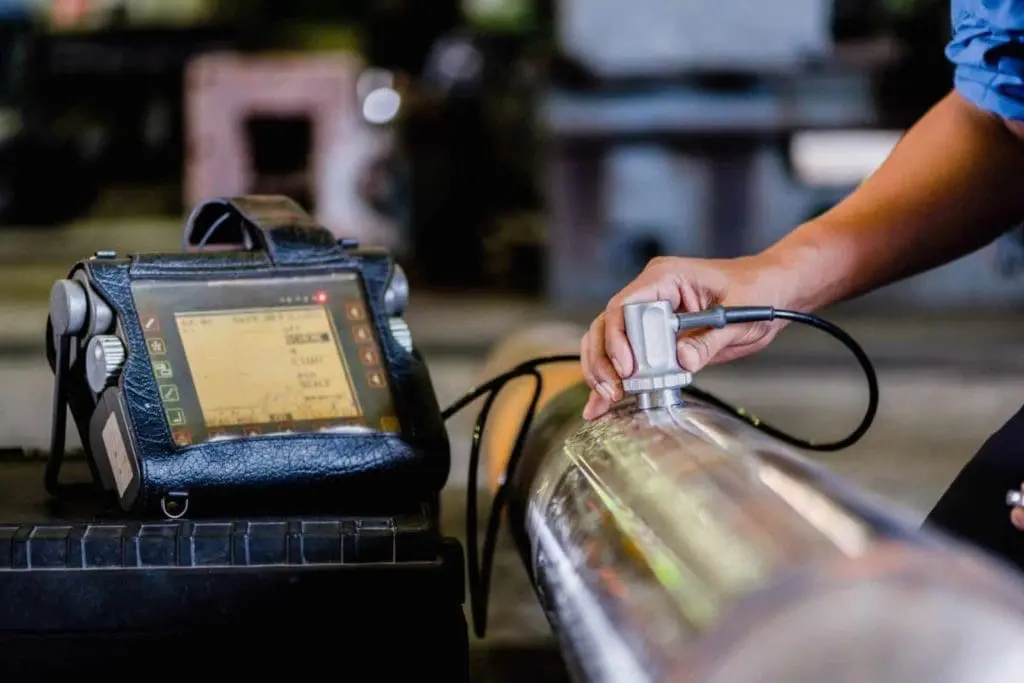
Where Do You Find Intergranular Corrosion?
Intergranular corrosion occurs in many different materials, such as aluminum alloys, stainless steel, and nickel alloys with copper, chromium, or molybdenum. One cause is an uneven distribution of alloying elements, which can cause variations in the electrochemical potential in the material, promoting galvanic corrosion. This uneven distribution also means that some regions are poorer in corrosion-prevention compounds, leaving them more susceptible to corrosion.
Al-2024 and Al-7075 often experience copper aluminide precipitating to the grain boundary, which reduces the corrosion resistance of the region. Other susceptible aluminum alloys include Al-5083 and Al-7030.
Unstable austenitic stainless steel 316 and 304 may undergo intergranular corrosion. Chromium carbide will precipitate to the grain boundaries, sensitizing the steel.
Nickel alloys, as mentioned above, can become susceptible to intergranular corrosion when exposed to hydrofluoric acid, chromic acid solutions, or sulfuric acid. Nickel-chromium alloys can never be used in corrosive environments due to their high susceptibility to an attack.
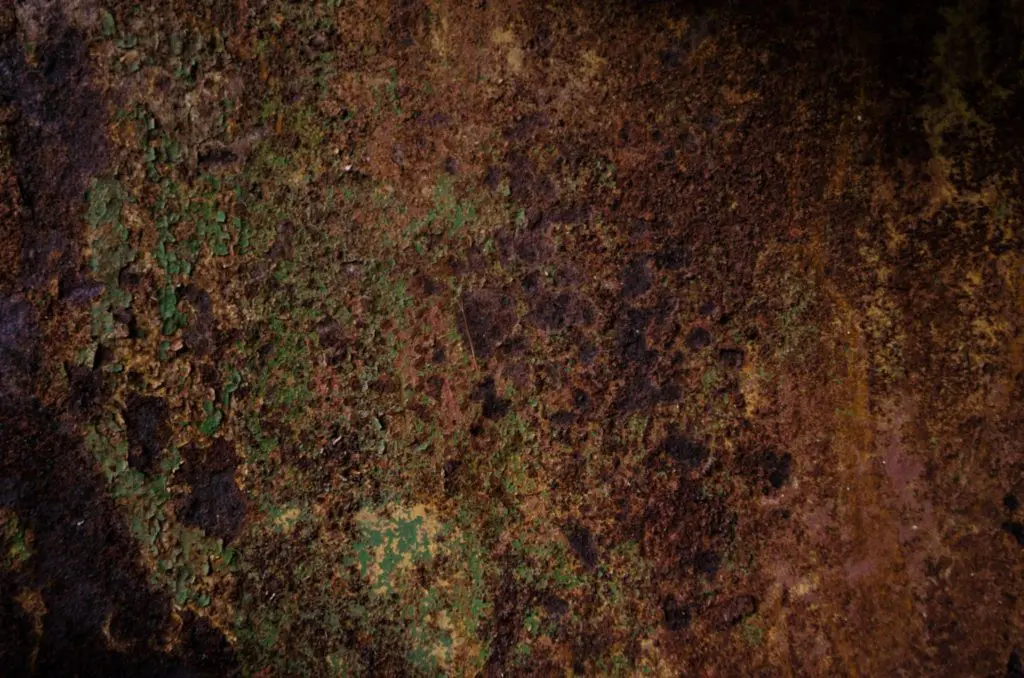
Other Types of Corrosion
- Surface corrosion: a uniform attack where a chemical or electrochemical reaction deteriorates the entire metal surface
- Exfoliation corrosion: a type of intergranular attack that removes layers of the metal in a “peeling” fashion
- Galvanic/dissimilar metal corrosion: two different metals in a corrosive electrolyte form a galvanic couple that corrodes the sacrificial anode faster than normal
- Microbial corrosion: microorganisms oxidize a material and worsen existing corrosion by depleting the water of oxygen, hindering the formation of oxides that otherwise protect against corrosion
- Filiform corrosion: water vapor breaches a painted or plated coating and starts creating small defects before propagating
- Environmental corrosion: interaction with specific chemicals or temperatures can lead to corrosion, fatigue, and fracture
- Stress corrosion cracking: susceptible materials that undergo high tensile stress in a corrosive environment will experience a rupture of protective oxides, lose corrosion resistance, and have crack propagation
- Pitting corrosion: localized corrosion where a point forms a corrosion cell on the surface that grows into a cavity
The most common types of corrosion are transgranular, meaning they occur in the grain. You can find transgranular corrosion occurring in ductile and brittle materials, and it is less catastrophic than intergranular.
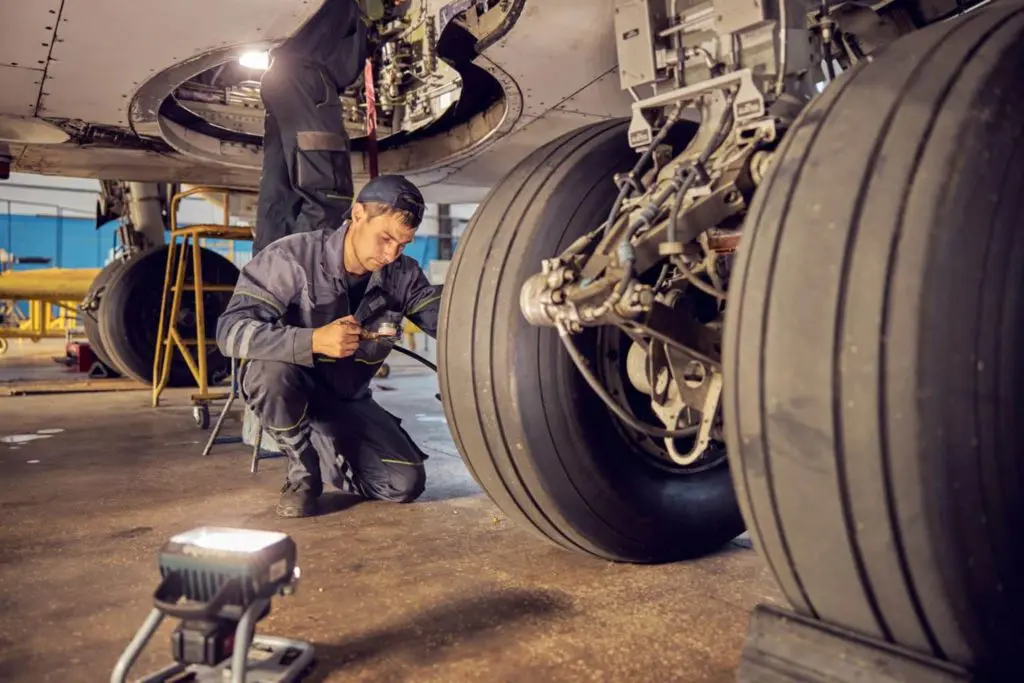
What Are the Dangers of Intergranular Corrosion on Aircraft?
When intergranular corrosion becomes visible, your part has a substantial crack in it and may fracture. This catastrophic event only appears in poorly-designed components, but it is extremely dangerous.
A catastrophic part failure caused by intergranular corrosion on an aircraft could injure or kill anyone onboard. Even absent such events, the aircraft must be taken out of service to repair the component and make the aircraft airworthy again. Furthermore, part failure can lead to mechanical damage to pipes, valves, engine crankshafts, landing gear, and pumps.
Toxic fluids may also leak through the corroded component, which would harm anyone surrounding it. These damaged pipes can also contaminate the liquids they are transporting.
How to Prevent Intergranular Corrosion
Unfortunately, intergranular corrosion isn’t obvious in a casual visual inspection like the powdery deposit of some other corrosion mechanisms. The use of x-rays or ultrasound may be required for non-destructive testing. If intergranular corrosion is detected, you can work with us at Mid-America Aerotech to receive fast repair services to keep your aircraft safe. Our cold spray technology can save you significant time and cost. Reach out for a free quote today.